Articles
How to Reduce Manual Handling Risks
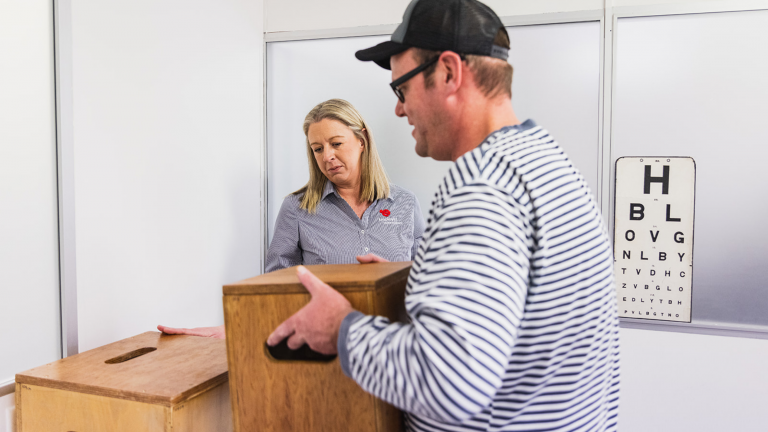
Manual handling is common in many workplaces. Unfortunately, so are manual handling risks. Without proper training and mitigation measures, employees can become injured and have major impacts on their lives and your business.
Employers can take steps to minimise manual handling risks and prevent injuries. With training, education, and proactive management, you can make sure your employees and your workplace are safe.
What is Manual Handling?
Manual handling on the job is the work that requires pushing, pulling, lifting, moving, or carrying. For example, workers in a factory that load boxes on a truck are engaged in manual handling. Similarly, workers that move furniture or push heavy carts are engaged in manual handling.
Your worksite may also involve hazardous manual handling. Manual handling becomes hazardous when it involves sustained high force, sustained awkward postures, handling people or animals, or unstable loads. These may pose a greater risk than normal manual handling, but similar mitigating measures can be used for both.
These manual handling movements are common across industries from construction to manufacturing to healthcare. For many employees, they are unavoidable. However, they can be performed safely and efficiently to preserve the health of the employee now and into the future.
What are the risks of manual handling?
Manual handling movements can pose many different risks. The severity of the risk is often dependent on a number of factors such as the type of movement or the intensity. Frequency also adds to risk; movements done daily pose more of a risk than those done only once a month.
The most prominent risk of manual handling are musculoskeletal disorders (MSD). These are injuries to the musculoskeletal system and its connective tissue. Common MSDs include:
- Strains
- Sprains
- Back injuries
- Hernias
- Chronic pain
- Soft tissue damage to the wrists, arms, shoulders, neck, or legs
For example, carpal tunnel syndrome from heavy computer work is a MSD. Straining the back while lifting heavy boxes is also a MSD caused by manual handling.
Once employers understand these risks, they can take steps to reduce them.
How to Reduce Manual Handling Risks
One of the first steps to reduce your manual handling risks is to understand where they exist in your workplace. Some may be obvious but others won’t be. This is when it’s helpful to engage a professional. Our team can help you identify and assess manual handling risks across your worksite.
Once they are identified, the best way to minimise those risks is through manual handling training.
Manual Handling Training
Manual handling training is training designed specifically to teach workers the safest and most efficient way to perform the various movements of their job. Training, like the one conducted by EDHS, is led by a licensed occupational therapist who teaches the basics of biomechanics.
Employees are taught not only how to lift, push, or pull safely, but also the theory behind these movements. This allows them to take charge of their own safety and feel empowered in the workplace.
Each training session includes a brief overview of anatomy and physiology and the effects that manual handling can have on the body. Employees are then taught proper techniques to lift, carry, push, pull, anything they may be doing on the job.
The most effective training courses are tailored specifically to the unique risks present in your workplace. When employees are equipped with these techniques and knowledge, they are able to perform their job duties more safely and efficiently, reducing your risk of manual handling injuries.
Manual Handling Practice
Training is a critical piece of reducing risks, but that training is only useful when applied to the real world. The more practice employees have moving safely, the more it becomes second nature in their jobs.
After the theoretical portion of training, it is recommended that employees be able to practice what they have learned. Under the guidance of an occupational therapist, workers can practice lifting properly, pushing efficiently, even standing with proper posture. This solidifies the principles they learned in training and emphasizes a ‘safety first’ culture in the workplace.
Through practice, employees can feel confident working safely and demonstrating correct techniques to other employees. When safety is a priority to all, manual handling risks are significantly decreased.
Proactive Management
When training and practical experience are available, all that’s left to do to minimise manual handling risks is be proactive and consistent. Initial training is a great start but be sure to provide regular refresher training as well. We recommend holding a manual training session once per year. This keeps the principles fresh in employee’s minds.
It’s also important to hold training if new job duties are added or aspects of the workplace change. For example, if you acquire new equipment or a new process is implemented, evaluate what manual handling risks these changes pose and provide training accordingly.
Make sure that employees are regularly practicing proper manual handling and helping others to do so as well. Make it a priority in the organisation from the top down. Before long, safety will be a natural part of your company culture.
Manual handling risks will always be present, but that doesn’t mean you can’t manage them and protect your staff. With a few simple steps, your business and employees can enjoy a safe workplace.